Update, the original astable self oscillating h-bridge is working well. This is now well into the most complicated breadboard system I've put together

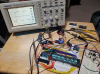
Measured, 5.03VDC in under load, 4.87VAC Cyc RMS shows on oscilloscope, with 10.2Vp-p at ~505Hz +/- 10. Hovers right around 75mA under full operation (+/- 0.5mA). The waveform stabilized (less jittery) under full operational load.
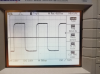
I have not added inductors yet, and I don't have any 2Ohm resistors to work with (although I probably have some 1/4W 1 ohm ones, I guess I could tie 2 together to test). I do have some 1812 SMD 22uH though, should I try one each of those in series with the positive emitters to help? Or would you still prefer one of the two later designs? I'm happy with this one so far, but I don't know what it means for the longevity of the VFD.
I had an error in my original code due to misunderstanding some awkward wording in the datasheets. Now, at 30VDC grid, and no awkward delays to avoid the bad ghosting I had before, with no blanking, the brightness is quite acceptable and the background is quite clean. I don't know if I need to do any blanking. There's the tiniest amount of ghosting from the previous column, but I have to look hard to find it.
Noritake did finally get back to me, they have asked me not to share the datasheet (the previous snip was what I retyped myself), but they are interested in the results of my tinkering. If anyone is interested they welcome to ask them on Twitter for the datasheet directly and they will provide.
Oddly, with my oscilloscope attached and the computer USB attached, something strange happens. The waveform gets destroyed and almost entirely negative, and an odd buzzing comes from the 5V switching regulator. The brightness also increases ever so slightly. This only happens if the USB cable is connected, or even if only the USB ground is connected to circuit ground

.
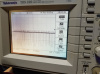
If I disconnect the oscilloscope ground, the perfect waveform returns at only half strength (2.5VAC but the display brightness doesn't change). It's the same as if I probe either side of the bridge to ground, instead of across both sides of the bridge.
I also found that one of my DS3231 boards appears to be a cheap knockoff and defective (not that I expected real ones when buying them on Amazon for $2ea) and my Arduino nano internal oscillator seems to be off by enough to be 0.14sec slow every minute... I'm starting to think that maybe I should separate this out into its own thread
