Some points:
1) An exterior ground plane is much better than an internal ground plane. They are typically both thicker and are less insulated from the ambient air.
2) For standard 1 oz. copper you don't get much more benefit from an area of more than about 1 square inch. Beyond 2 sq. inches on a single layer there is no noticeable additional cooling.
3) It is far better to connect two external copper pours (on opposite sides of the board) of about 1 sq. in. using thermal vias than it is to have a single copper pour of 2 sq. in.
In these pictures the top pour is about 1.5 sq. in. and the bottom is 2 sq. in. and are connected with 99 vias. This provides much better cooling than would a single plane/pour of 3.5 sq. in. and in this particular case we have about 25C per watt given free air circulation (measured).
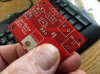
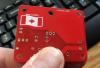