As with all simple projects, I'm back like 2 months later and asking for advice. After all the horror stories about not enough power I put the 4 ~500W quarts elements in and the 1000W metal cased element. The plan was to only use the metal one in the beginning as a boost as it would retain it's heat when I went to the quartz elements, I don't have 3KW at my outlet anyway. The boost element was unneeded and made PID awful to tune. So i removed it, good thing I spent so much time modifying the program for it.
I started with the code from git "Tiny Reflow Controller" changed the thermocouple controller, added menus to change the all setting and store them to eeprom instead. Had to switch to a ATmega664P as the 328 was out of memory for the oled display even with stock code, libraries have changed I think. I am not a programmer, so this was a large portion of the problem.
Just thought I'd share and ask for advice here. I've been looking into adding "take back half" as an improvement, but I don't think that is going to fix the overshoot much, if any. I might removed the insulation under the oven chamber to dissipate some heat build in the steel under the elements. Or switch to 4 500W halogen bulbs.
The bottom half of the chamber is steel and the top aluminum flashing. Surrounded with ceramic insulation. I had to shorten the quartz tubes with a diamond wheel. Was trying to mount the chamber and used sheet metal screws as stay bolts, if it's good enough for a steam engine boiler... lol.
Here is a graph of my results. I added a preheat ramp 2C per sec (here it is set to 125C) as the original code just switched the elements on and I got a 9C per second rise. Then code then ramps up to 200C which then triggers the reflow portion, that is still original code. Then I changed again to a ramp 2C per s until the original code cuts off at the 250C set-point -5C.
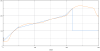
I think the tune is as close as I can get it. But a 25C overshoot is almost guaranteed, or cutoff early and coast up to the setpoint. Maybe add cutout parameter to shut the heat down early and then catch it when it levels off? So am I screwed and need to change elements, or thing this can be made close enought? Thanks.
I found this and needed to share it here
According to Linear Technology’s Jim Williams, “The unfortunate relationship between servo systems and oscillators is very apparent in thermal control systems.” (Linear Applications Handbook, 1990).
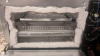
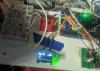
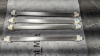