I'm setting up some logging stuff to compare the Talyvel and the NASA tiltmeter outputs over a few days.
I thought that the following might be of interest. For anyone who wants to understand how the circuit works, read this article:
https://aip.scitation.org/doi/abs/10.1063/1.1685975Here is a screenshot showing the behavior:
The pink line is the voltage at the top junction of the bridge, relative to ground. This is just the oscillator, 10Vpp.
The yellow line shows the voltage at the sense capacitor which is charged by the oscillator when the oscillator is positive. The white curve is the (magnified) difference between these, which is the voltage across the diode that charges this sense capacitor. A positive voltage means that the diode is conducting (forward biased).
Start from the second crossing of the pink and yellow curves. At this point there is no current flow through the diode. As the oscillator voltage continues to rise, the diode begins to conduct, and the voltage on the capacitor rises, following behind the oscillator. Eventually the diode swings into full conduction, and charges the capacitor, with about an 800mV drop. After the oscillator peaks, the voltage on the capacitor would remain fairly stable, but then is discharged by the second diode. The article shows that if diode drops are neglected, then in the steady state the two capacitors end up with the same average amount of charge, so that (Vp + Vdc) C1 = (Vp - Vdc) C2, where Vp = 5V, Vdc is the output DC voltage of the circuit, and C1 and C2 are the capacitances of the two sense electrodes. Hence Vdc = (C2 - C1)Vp/(C1+C2). Here the value of C2-C1 can get to about 10% of C1+C2.
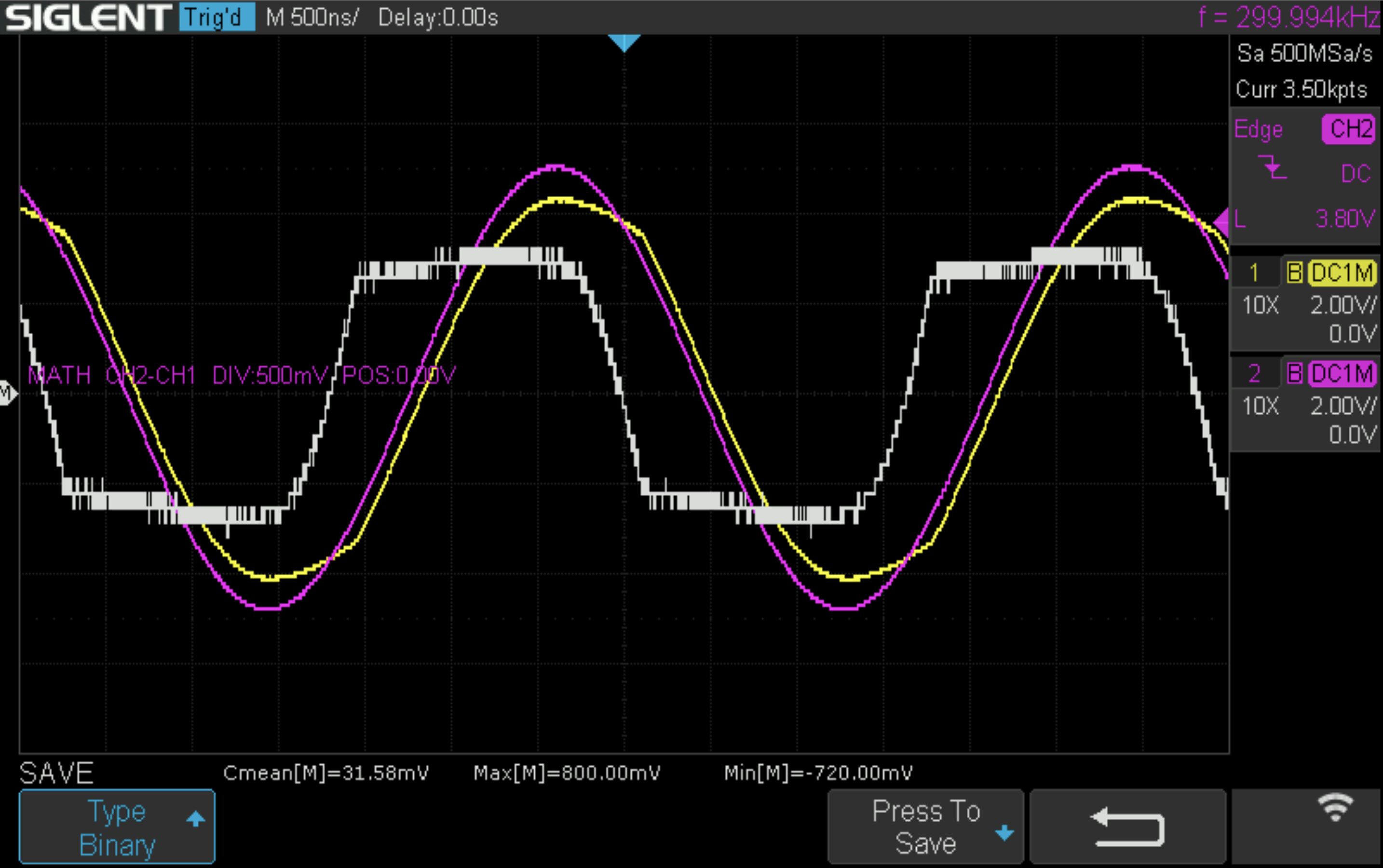