does anyone have any nice welding clamps or fixtures they made?
I got an idea to make chill bars. I got a aluminum block, a big one. I see chill blocks are like 900$+
I thought it might be pretty simple to setup some stops on the table saw, then cut a T - shaped groove in the middle of the block. So long the stops are proper (magnetic switches), I think the saw should be able to widdle out a T shaped slot.
Then, I would put end plates on both sides of the brick with the T in it (glue or screws) to seal it up without the need for any milling machine.
For the gas diffuser I thought to get two brass tubes of the correct thickness for the bottom of the T slot. Solder them together like a double barrel shotgun and then cut the top tube in half, so it makes a U on top of a O. Then drill holes down the middle of the U (cut pipe) to make a gas diffuser that has nice rounded walls. Then just stuff it into the hole, throw in a segment of drilled copper on top to cover it up, and maybe stuff a rolled up tube made of out screen material under the copper to act as more of a diffuser.
I see alot of people make this but I ain't see one with plates on the end, so that means you can use a saw to cut the whole thing. The thermal conductivity and stiffness increase from having machined side walls instead of just putting plates on the sides is bull shit IMO.
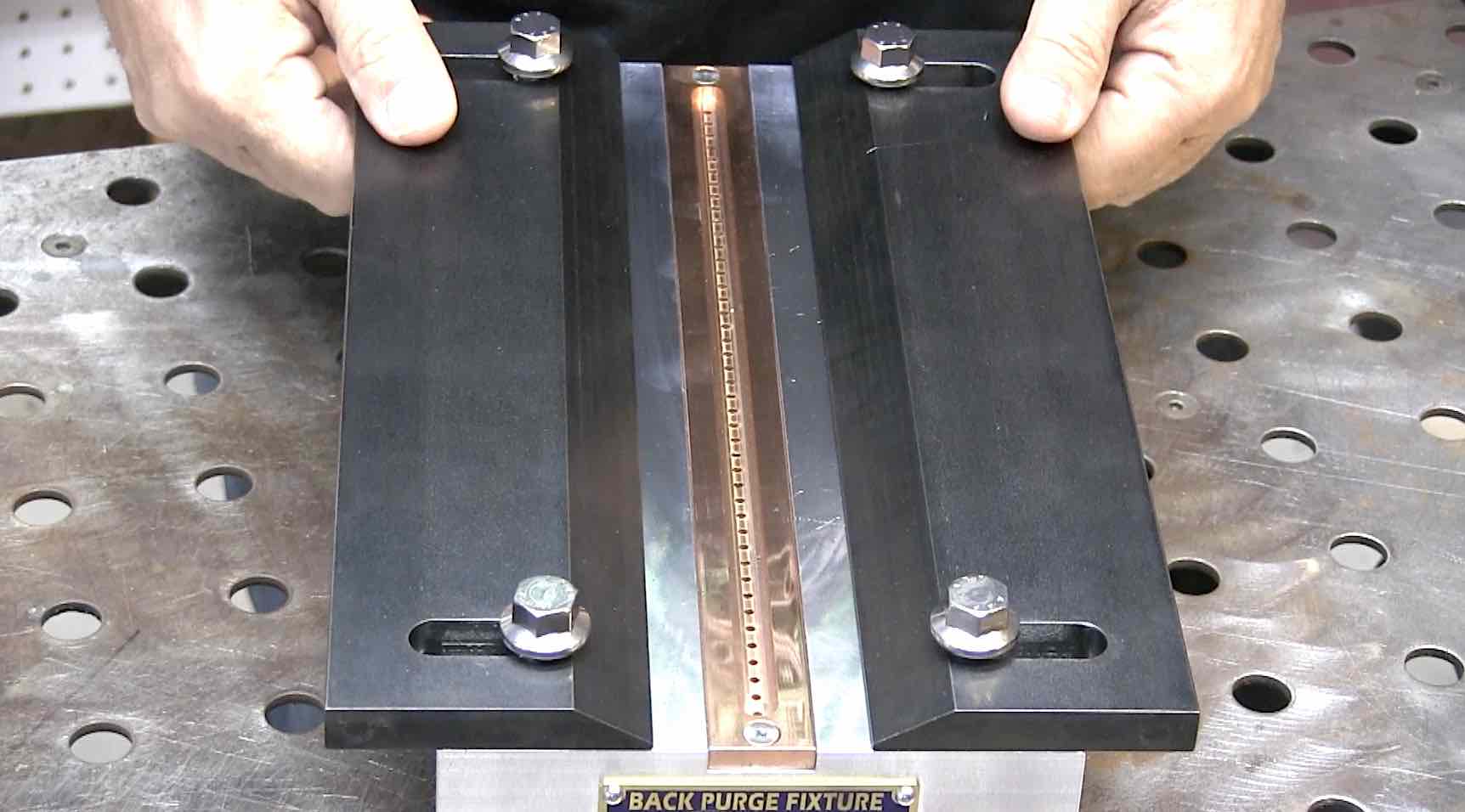
What I am saying is that if you just put walls on the sides made out of plates it gets rid of alot of complex milling.
The only hard part would be to cut slots on the top steel pieces to hide the screw heads, and the small slot in the middle of the copper bar. the slot in the copper bar I could do on my tiny milling machine though. But other then that so long you have a block of aluminum I don't see the exact need for a mill. Lots of grinding to bevel the plates though. I got a aluminum block, a steel flat bar (5/8 x 2.5) and copper bus bar and even brass tubes. I could try a angle gouge on the top plates to rough it in before precision angle grinding.
But shit, is almost free for me if I do it this way. I wonder how the saw stands up to a aluminum block. If you only do a mm at a time I think it will hold.

and maybe make a copper epoxy cement by mixing copper powder with epoxy to anchor the tube into place and increase thermal mass, but idk if you want the tube coupled to the block because the gas is coolant and it would be cooling the block but it would be emerging hot on the weld vs not cooling the block as much and directly cooling the weld.

a regular slot and a copper plate to cover the whole surface would work. there is no need unless you are trying to save copper. i cant think of a reason.