Thanks for the practical examples helping novices how to work with Acq.ON more (Sequential).
That was the thing I was trying to figure out this week by it was not intuitive and the manual didn't help from the first try.
Could somebody advice on how use 1204/1104xe for tracing a problem witch require ideally "data logging" of 2 hours the turn marker of 200-1500 RPM rotating shaft.
I am able to check with a scope that in ideal conditions turn marker only one pulse per turn. But equipment tends to give not systematic failures over 1-2 hours of work cycle.
There is the idea that either some voltage fluctuations at line \ ground or vibrations (or both) make false/absent rotation pulses.
Ideally, I need to get 1-2 hours triggers on all pulses and save that data to compare with a time of equipment errors in the final image (equipment is drum scanner and faults to trace are "dead" lines of pixels in the final scan that appear not always and so still are not identified by source).
I was reading in the manual for older Siglent scope model _CML about RECORD function where it is possible to write all untriggered screens with specified time intervals up to 2500. Could 1204xe make such a trick in some mode - it has much better memory than _CML scope model?
CML Record function is very extremely different what is in modern SDS1000X and X-E series.
CML records TFT frames, up to 2500 and with user settable interval. (There is also "Recorder" in CML but it have 6M memory and it can record low samplerates continuously up to 6Msamples, but it is so very long time I have used CML that it is better I do not try tell how it works.
SDS1000X-E
It can save up to 80000 trigged waveforms. (normal mode to wavefrom history buffere FIFO, woreking always in bacround. OR in special Sequence mode to this same history buffer. In sequence mode scope do not handle any other processes what may lead to loose some trigger event so it also do not display during this Sequence until whole sequence is ready)
Odd but still principle itself is valid.
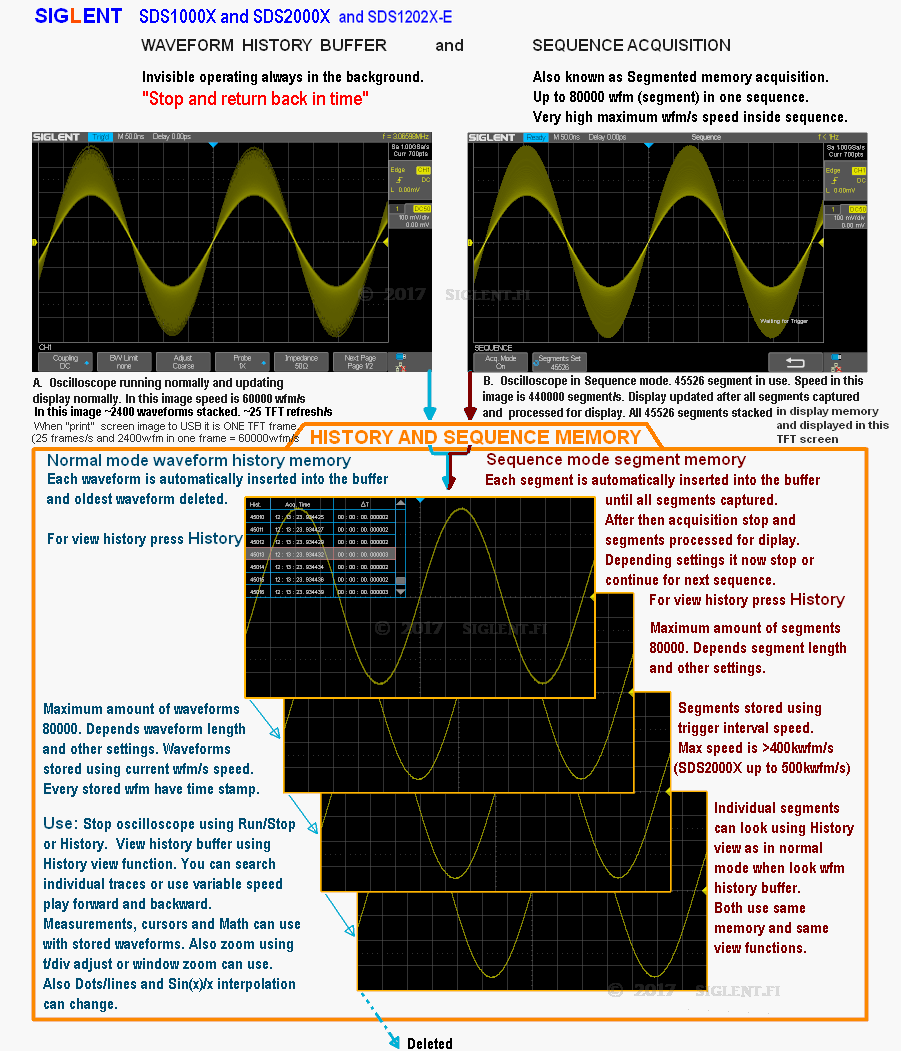
Old but principle itself is still valid.
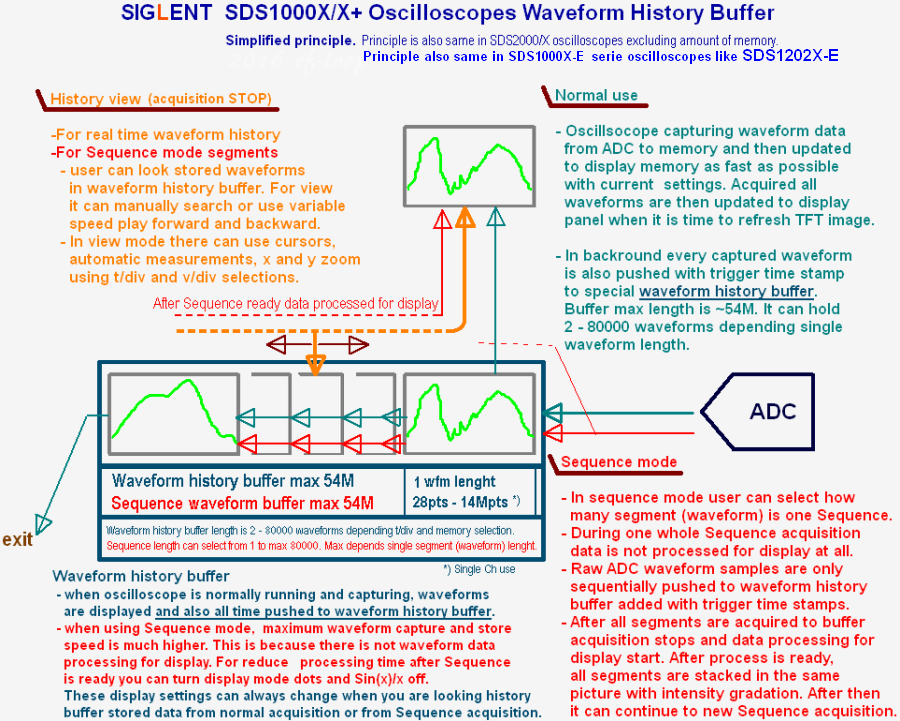
Next image show amount of history and sequence mode segment memory
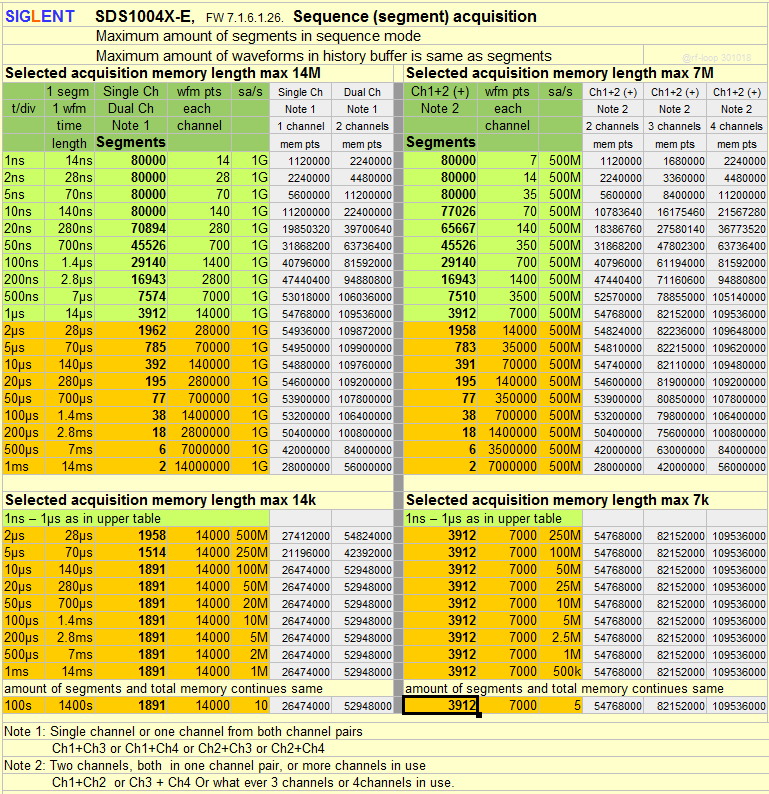
How ever acquisition is made to history buffer (normal or sequence mode)
Every single acquisition (every single horizontal sweep) is time stamped. If there is 80000 or 2 acquistions in buffer every have time stamp (but there is not real time clock in system so time of clock is not true time but time between acquisitions is accurate)
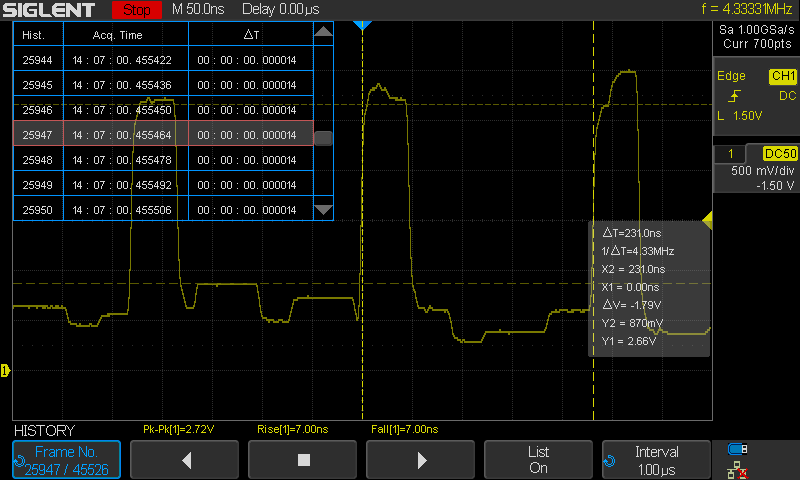
(example of time list. User can select what segment (frame) he want look. Also it need note that this do not save image memory, it save ADC data and every segment (frame) is current memory length in use. This is why all can post process including interpolation and math and measurements, even run mask test.
----
But now your problem.
If you want only record time interval list when trigger have occured (scope have detected pulse) you can record 80000 time stamps.
Just set scope to trig this pulse. Set trigger so that it trig when pulse signal meet some your specified values.
For max count of events. Then set scope for 10ns/div and select sequence mode with max 80000 segments. Yes in this case waveform length is only 140ns. You can not see your pulse (perhaps part of rise edge or?) but every time it meet trigger, it make acquisition and write time stamp for it.
But, now, even with this if your speed is constant 1500rpm and one pulse per turn you get 80000 time stamps. 80000/1500=53,3 minute. With this speed, over this time you have time stamp (including time after last event aka interval) from every single trig. You can watch if there is missing trig (missing pulse as trigger setup have defined what us "pulse").
But not alone this. Other channel(s) can also be in use and also data from these is saved same time (example one may watch some point voltage etc)
But then, if you want also see your whole pulse there need use much more long length for one acquisition.
If think your max speed even with this 1500rpm one turn is 40ms. I do not know anything what kind of sensor you have for pulses and how long is your pulse with minimum and maximum speed (200 - 1500rpm) perhaps we talk milliseconds.
This is only imagination. If think your pulse width 36th of turn (10 degree) then pulse width is roughly between 10ms to 1ms.
Ok, perhaps then 1ms/div is ok for look whole pulse.
If want look maximum amount of pulses what can record using normal history or sequence mode. If reduce memory length to 7k and t/div is 1ms and then sampling speed is 500kSa/s (samples interval 2us). Maximum amount is 3912 this kind of waveforms stored in memory (in 4 channel model 4 channel parallel)
with 1500rpm this is only 2.6 min. and 200rpm it is 19.5 min. (but of course time resolution is still good and lot of more than needed)
But this is not alone what can do. But this is not for your case.
Example. If want longest record, lowest samplerate and with some time gap between records
It can do (extreme limit) 5 sample per second
Limit memory length (acquisition length) to 7k
Set 100s/div
3Now one acquistion time lenght is 100s*14 = 1400 seconds 23
1/3min
and now it can also record 3912 of these, total 63 days long sum of data but total time more. As told, between these 23
1/3min records there is gap. I have not checked now and I'm not sure if I remember right but gap is around one horizontal div so in this case ~100s gaps. So total time is even more than 63 days
Of course selecting optimal time base and optimal one acquisition length there can fid solution for many kind of needs, but of course not for all needs.
Old times I have been working in factory where we need always analyze and find some mysterious errors in lot of different machines and processes. Of course there we have analog and digital data recorders, scopes, spectrum analyzers and so on... of course because if manufacturing stop due to some failure in machines it is hundreds or "sky is limit" times more expensive than some electronic test equipments. But still, in many cases. Because time is money and specially, "less time = save more money".
There was golden rule. Do it simply! Do not waste time for finding this and that and for nice analyzators and scratching head how I use this for remove this problem in important machine.
One solution is that you install reliable extra detector one pulse per turn . (what ever even simplest but reliable, example some proximity sensor) then trig scope with it and watch that with every this pulse appear also this pulse what you suspect. After you find more what happen there you can analyze just this situation where failure happen, example watching some drop outs etc.
With extra sensor you can even simple trig only when it fails.
Of course if your shaft speed is constant this is extremely easy just with normal trigger functions without any extra but your speed change between 200-1500rpm so this need some things what can "remove" this speed change affect. One is just extra sensor. Most easy if you have available it.
But then, do you like analyze it because analyzing something is so nice... or repair it now or better if yesterday....
Example about other kind of thinking. Of course this is trivial example and perhaps not at all for your case... but some times we need break thinking some locked or circle paths in our brain and find other thinking paths for find solutions. Some times solutions are even extremely simple after it pops up.
Think example what happen there when one pulse pulse is missing. What it do in this case and can you use this information... you know digital scope is always doing pretrigger sampling until trigger... so you can easy get what happen before something has happened. If you can detect (failure) result then you can analyze what happen before... just tip for change thinking method to reverse (cousin of this is negation test in thinking process)
For siglent there something in wish list.
100s/div is now slowest.
It can change to 1000s/div or even 10000s/div (roll mode 100Sa/s and normal mode 1kSa/s)
This need only some bytes in FW.
Some competitors have it.
There have been many times some questions about more long time data recording.
Even with these extra slow sample rates it can directly save continuous wfm to USB. There is now lot of processing power for it.
It was long long time ago even SDS1000CML can do it when very slow samplerate, directly to USB (I do not know when they have take it off)
Now there is processing power, SDS1kXE can easy do much more this kind of things. More slow t/div andf also direct unlimited length capture to USB if sample rate is enough slow.
It is not only one people who need more long capture times or even like very long time data logger without time gaps.